数控高级技师论文第四篇
摘要:介绍了铝合金圆棒气滑铸造原理和特点, 设计制造了一种能铸造较大规格的铝棒气滑结晶器, 并在调试出合理工艺参数后, 生产出满足企业规格和质量需求的产品。
关键词:气滑; 结晶器; 铝合金铸造;
铝作为地壳中含量最丰富的金属元素,具有密度小、重量轻、强度高以及价格适中等特点,被广泛应用于各个领域。近年来,随着国民经济高速发展,在国家大力提倡节能减排背景下,铝合金需求量越来越大,对型材品质和性能要求不断提高。因辽宁忠旺机械设备制造有限公司生产需求,急需研发一种规格φ343的气滑结晶器。
1 气滑铸造原理和特点
气滑铸造是目前世界上最先进的铝合金半连续铸造技术之一,其原理是在结晶器上分别开孔,铸造油和压缩空气通过管道输送至结晶器相应孔中;然后再进入石墨环中混合,在石墨环内表面形成油气膜。熔融铝液在石墨环处一次冷却凝固成壳,随着铸机下移,铝液不断充满凝壳;结晶器喷出的水对凝壳进行二次冷却,凝壳内部熔液逐渐固化,形成铝棒。
由此可见,气滑铸造具有如下特点。
第一,石墨环内表面油气膜可使铝液快速固化,产生最低限度的合金偏析,从而减少凝壳厚度和液穴深度,获得晶粒更小、组织更均匀的铝棒。
第二,由于油气膜隔绝了铝液和结晶器接触,所以可获得更光滑的铝棒表面。
第三,铸造油和冷却水使用量较少。
第四,铸造速度快,生产效率高。
第五,后续工序优化,为企业带来更大的经济效益。
第六,铝棒规格越大,加工和制作难度越大,对结晶器及其配件性能要求越高。
2 结晶器的设计和制作
结晶器结构设计详图如图2所示。本结构是在美国Wagstaff公司设计的结晶器的基础上,针对大规格气滑结晶器的特点进行了优化。
图1 结晶器结构示意图

1.结晶器本体;2.隔水板;3.密封圈;4.压盖;5.转接板;6.石墨环
由图1可知,1结晶器本体采用6082铝棒经五轴数控机床加工而成,以保证其必要的强度和精度;2为5系铝板制成的隔水板,可起到过滤冷却水中杂质和调节水压的作用;4转接板和5石墨环均采用进口品牌产品;4压盖将转接板压紧,并通过密封圈3密封,以防止油气泄漏。
经试验,可得出以下几项数据:第一,结晶器整体最佳高度为149mm,有效冷却高度最佳值为39mm;第二,冷却水孔采用双排水冷却,一次冷却角度为45°,二次冷却角度为23°,该角度既提高了结晶器冷却效率,加长了铝棒表面泡核沸腾距离,又减小了水冲击铝棒表面后反弹水量与水速度。制造装配完成的结晶器如图2所示。
图2 φ343结晶器成品图
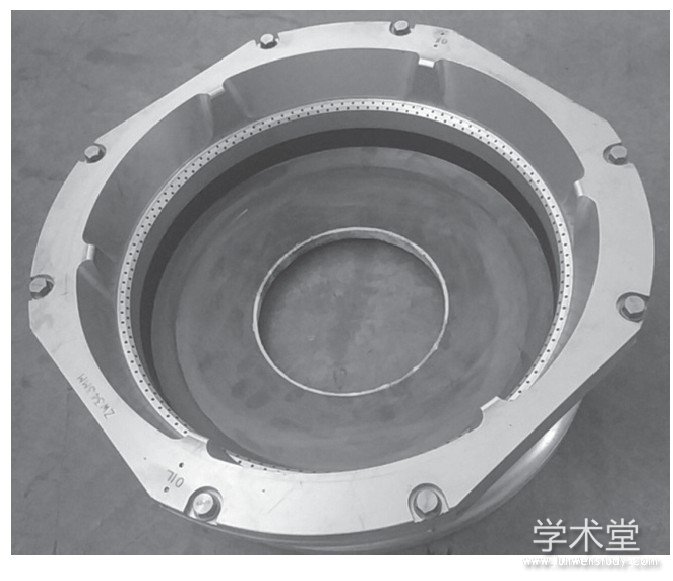
3 试验过程及结果
3.1 工艺参数设定
在与相近规格工艺参数比较后,设定了该规格结晶器初始工艺参数,如表1所示。
表1 φ343工艺参数

3.2 铸造过程及结果
铸盘各结晶器冷却水量较为均匀,开始铸造时盘首温度为690℃,稳态时盘首约为700℃,铸造成品率达95%,铝棒表面质量及内部组织均检验合格,可满足企业使用。成品铝棒如图3所示。
图3 铸造成功的铝棒
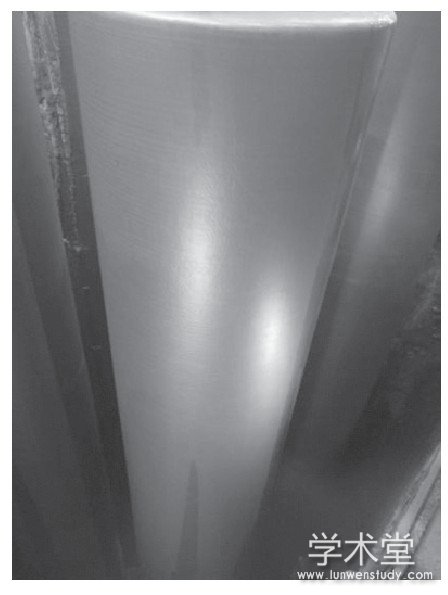
3结论
本次设计的结晶器结构合理,铸棒成品率高;工艺参数较为合理,铝棒表面质量及内部组织均能满足企业需求。由于铝棒直径越大,铸造过程中进入气滑状态的难度就越高。在本次铸造中有个别铝棒未进气滑,导致表面质量差,经分析其原因是在石墨环表面没有形成有利于铸造的油气膜,致使石墨环和熔体之间没有良好的润滑。因此,在下一步工作中,应调整工艺参数,使铸造气体压力和结晶器润滑油量匹配度更好;另外,应长期跟踪铸造过程和结果,积极发现问题,进一步提高产品质量。
参考文献
[1]罗启全。铝合金熔炼与铸造[M].广州:广东科技出版社, 2002.
[2]李小亚, 王东立, 许振明, 等。气膜成型连续铸造技术[J].特种铸造及有色金属, 2002, (5) :27-29.
[3]张建平, 乐永康, 欧斌, 等。铝合金气滑铸造技术研究[J].有色设备, 2006, (6) :1-3.
[4]王潇磊。铝合金油气润滑铸造装置研发和工艺研究[D].大连:大连理工大学, 2017.
点击查看>>数控高级技师论文(精选范文8篇)其他文章