仪表工程师论文第四篇
摘要:采用S7-200系列PLC作为下位机,研华工控机作为上位机构成管式加热炉PLC控制系统。充分利用PLC编程灵活、抗干扰能力强等优势,扩展了EM235模拟量输入输出模块,实现加热炉温度信号的采集和控制。同时,上位机可对系统运行状态进行监控,实现了良好的人机交互功能,在工业控制中具有一定的借鉴作用。
关键词:管式加热炉; PLC; 梯形图; 控制系统;
0 引言
工业革命以来,加热炉在生产制造领域一直占据着十分重要的地位。管式加热炉是对原油加热,为保证加热炉出口原油温度适应负荷的需要以及加热炉的运行安全,各个环节的工艺参数必须严格控制,最主要的控制参数是加热炉出口原油温度。这里设计了一种保证加热炉可靠安全运行的控制方案,控制器采用易于构成控制网络的PLC实现,PLC有着运算速度高、指令丰富、功能强大、可靠性高、使用方便、编程灵活、抗干扰能力强等特点。本设计利用PLC作为下位机;同时,采用MCGS通过上位机对系统运行状态进行监控,实现了良好的人机交互功能。
图1 控制系统硬件配置
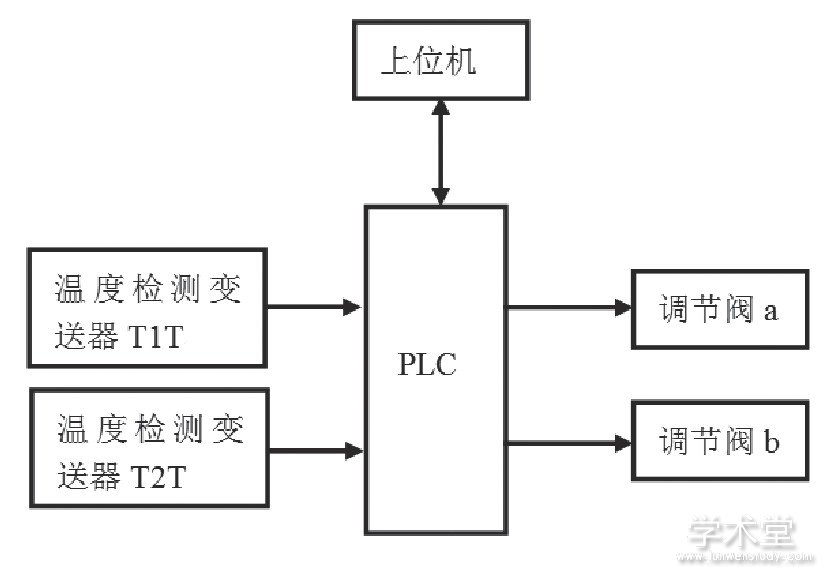
1 控制系统硬件构成
管式加热炉控制系统输入、输出点数较少,所以选用SIMATIC S7-200系列CPU224型PLC.控制系统包含上位机(MCGS组态监控软件)、下位机西门子S7-200 (CPU224) PLC、一个EM235模块、两个温度检测变送器,两个调节阀、上位机与PLC通过RS485通用串口线、RS232-RS485转接头相连接。控制系统硬件配置如图1所示[1].
2 系统硬件选择
2.1 PLC的选型
调节器用来接收温度检测变送器送来的信号,并且作出相应逻辑控制,然后再反馈到调节阀上去,形成闭环控制系统。PLC是一款既可以编程又可以逻辑控制的调节器,具有庞大的功能并且操作简单,利用梯形图编程实用易行。PLC选取西门子系列S7-200, CPU224(可外接7个扩展模块),利用PLC作为下位机,起到调节器的作用,与上位机通讯采用为PPI协议。S7-200与上位机MCGS通过RS232/RS485转换器与RS485通用串口线连接,保证控制器与监控软件的远程通讯功能与数据交互能力,实现MCGS远程监控的功能[2].
A/D转换器为FXZN-4AD;D/A转换器为FXZN-4DA.
2.2 传感器的选择
检测燃烧室内和出口处原油的温度,选择工业中常用的热电偶温度传感器来检测,它可直接将热信号转换为电信号,再由变送器变送为与温度成线性关系的标准电信号传输出去。热电偶选取两种材质各异的导体,由于热电效应的存在,在导体之间将产生热电势,根据热电势计算出实时温度的值。因为燃烧器的燃料是燃料油,加热炉燃烧室内能产生的温度在1300℃以下,燃烧室内温度传感器采用S型热电偶,量程为0℃~1300℃。原油出口处温度相对较低,选用T型热电偶,量程为0℃~350℃。
得到了温度的电信号以后需要将数据传送出去,并且标准化。因此,需要温度变送器,将电信号转换成与温度成线性相关的电流信号,传送给模拟量模块。STT250能够把传感器所得的温度信号线性的转化成模拟信号,它是一款两线制的智能元器件,可以将4mA~20mA的电流传导给与下位机相连的EM232模块,进行数据采集的信息传递。
2.3 调节阀的选择
调节阀b用来调节管式加热炉原油的输送量,通过接受控制器所给定的信号,实时地调整输送到加热炉内的原油流量,以应对炉内温度变化引起的加热精度的改变。调节阀a是用来控制燃烧器的燃料流量,此阀数值改变直接影响燃烧燃料产生的热能,减少燃料即减少能量转化,从而直接控制了燃烧室温度,间接控制了原油的加热温度。
调节阀的种类有3种,而此处需要加热的原油和燃烧器的燃料都是易燃易爆的物质,所以此处不能选择电动调节阀,适宜选择气动调节阀,简单方便,易于控制且安全性好。
表1 PLC I/O及软元件地址分配表
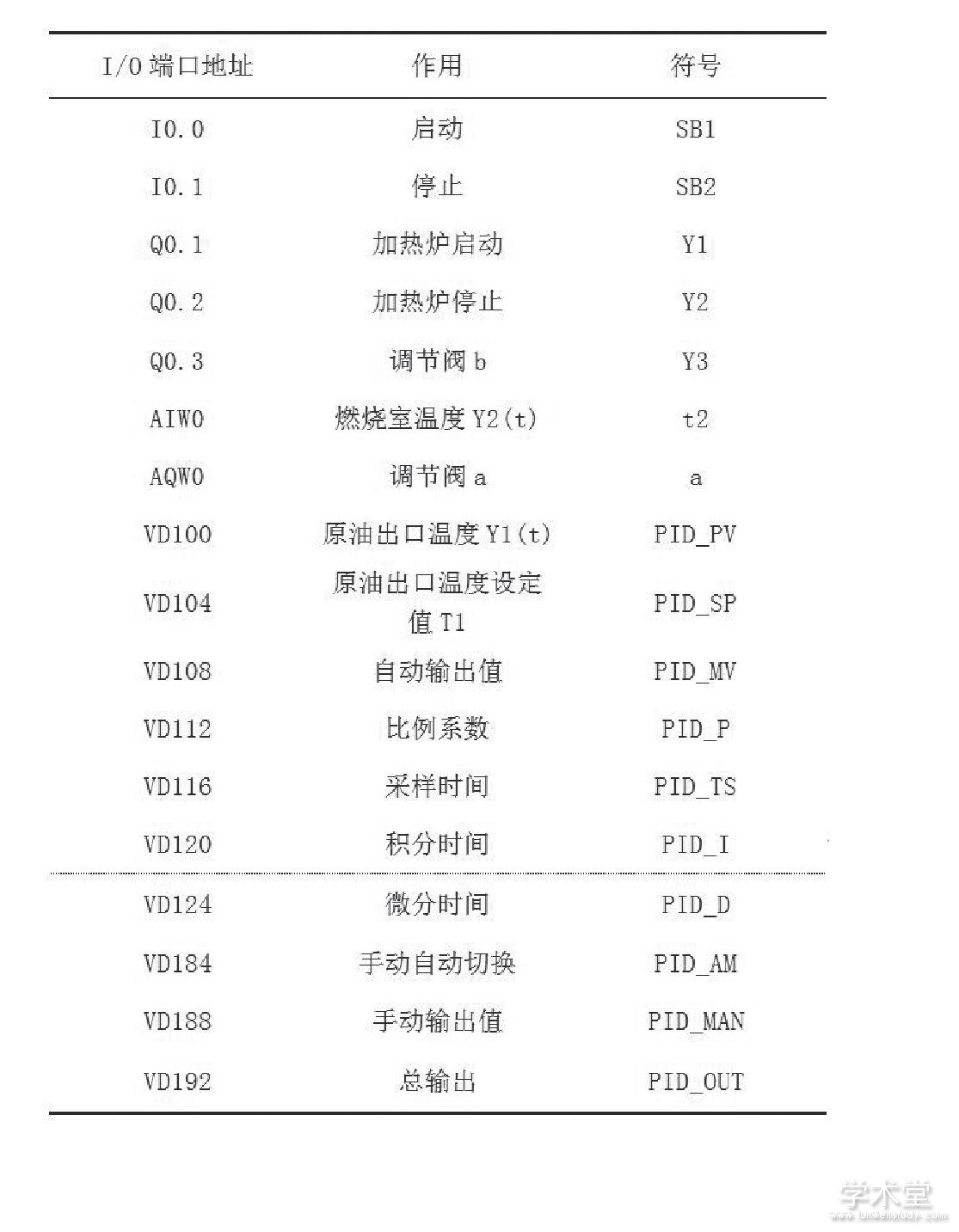
调节阀气开气关形式的选择要以安全为前提,当危险事件发生时,加热炉的燃烧器应该立即停止加热,避免温度过高发生爆炸,所以调节阀b选择气开式调节阀。出于对加热的原油下一道工序和加热炉精度的考虑,危险情况发生后应停止继续输送原油,所以调节阀a也选择气开式。基于此,调节阀的类型选择常见的单直通气开式。
2.4 上位机的选择
上位机选用台湾研华工控机,工控机主要配置为:Pentium III处理器,128M内存,15G硬盘。
3 PLC硬件设计
分析控制任务可知,数字量输入2个,分别为控制系统的启动与停止;数字量输出3个,分别为加热炉启动、加热炉停止、调节阀b;模拟量输入1个,为燃烧室温度;模拟量输出1个,为调节阀a;软元件10个,包括原油出口温度检测值和设定值、控制系统自动输出值和手动输出值、PID参数(比例系数、积分时间、微分时间)、采样时间、手动/自动切换输出等。列出PLC的I/O及软元件地址分配见表1.画出相应的I/O外部接线图如图2所示[3].
图2 PLC I/O外部接线图
图4 主程序
4 PLC软件设计
PLC的软件设计即编制PLC的控制程序,使用最多的就是梯形图程序,采用经验设计法进行。
4.1 控制系统流程图
燃烧室内加热采用的是燃料油,通过调节阀a调节燃料油流量以控制被加热原油温度,发送启动命令后,调节阀a打开并启动燃烧器开始预热,当燃烧室温度达到设定值时,调节阀b打开输送原油开始给原油加热,控制系统启动控制原油出口温度,加热炉正常工作。PLC控制系统流程图如图3所示[4].
4.2 梯形图控制程序的设计
主程序:将PID的参数传入到PLC的寄存器中,采样周期为0.1s,中断时间为100ms,积分时间为0s.主程序如图4所示。
图3 控制系统流程图
图5 温度采集程序
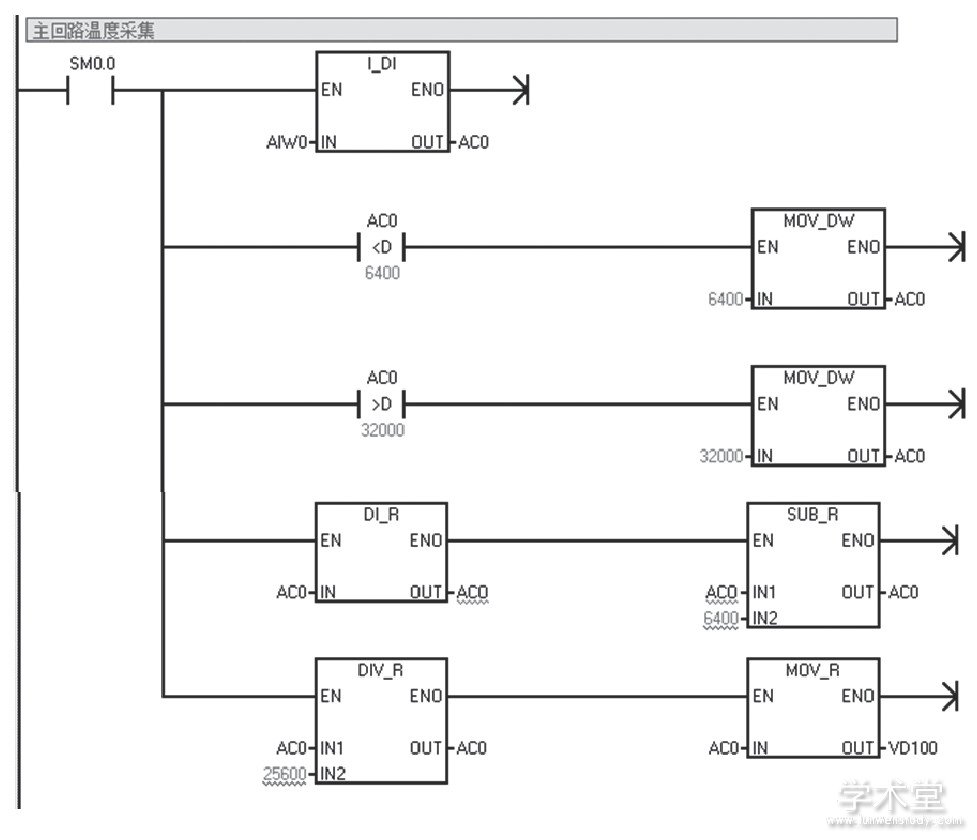
采集程序:将加热炉内的温度检测变送器采集的数据送到PID_PV中。温度采集程序如图5所示。
图6 输出处理程序
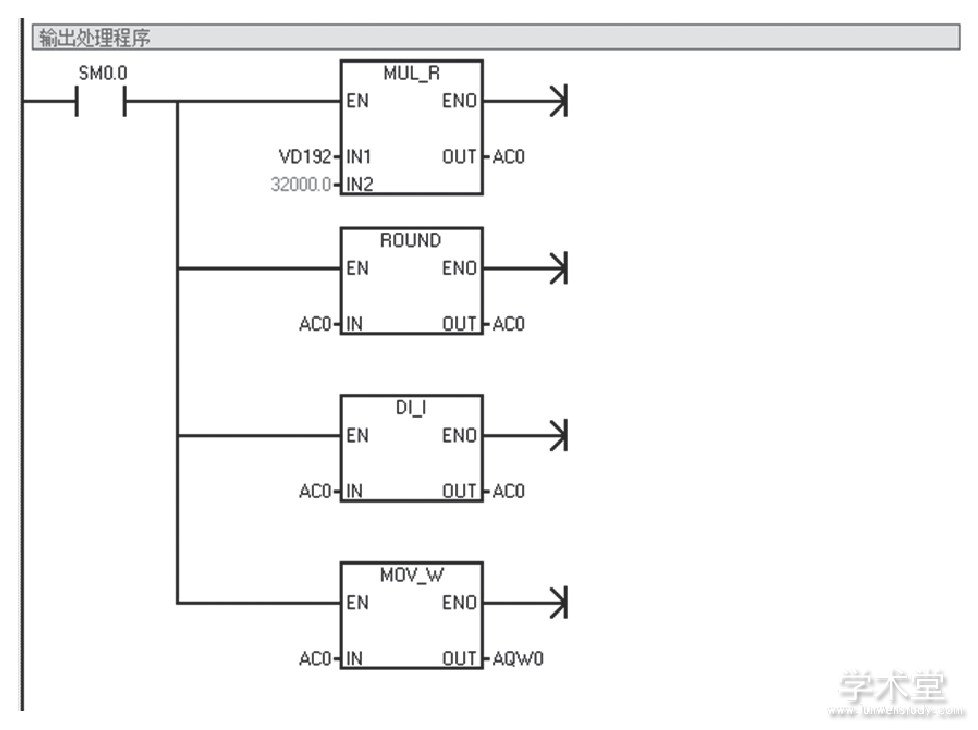
输出处理程序如图6所示。
5 结语
采用功能强大的PLC控制器实现下位机的控制,PLC选用了S7200-CPU224,并通过模拟量模块EM235实现温度信号的采集和控制,利用组态软件与PLC实时通讯,通过组态画面与工程画面实时掌控加热炉现场数据,并能及时调整参数,监控系统运行情况,可用于对石油加热的管式加热炉的控制,对其他工业控制亦有重要的借鉴意义。
参考文献
[1]许川佩, 彭圣华。基于PLC的自动化生产线控制系统[J].仪表技术与传感器, 2016 (12) :85-89.
[2]马学成。基于PLC和触摸屏的硬胶囊生产控制系统[J].工业仪表与自动化装置, 2017 (6) :97-100.
[3]魏静敏, 单冲。基于PLC的自动灌装生产线控制系统设计与实现[J].科技视界, 2013 (13) :56-57.
[4]王蕊。间歇式化学反应器分程控制系统的实现[J].现代化工, 2014, 34 (7) :157-158, 160.
点击查看>>仪表工程师论文(精选范文6篇)其他文章